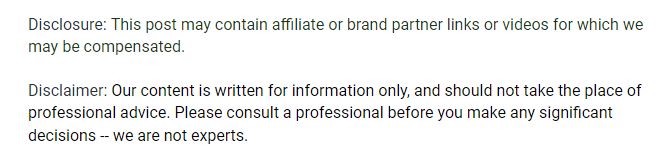
In the micro-filtration industry, one of the most commonly used materials is woven wire and screens. This means that regardless of whether the pores are the size of a human fist or microscopic, the primary objective of the filtration mechanism is to avail strong material that is non-corrosive, strong and flexible. There are different types of filtration media with the most common being the wire cloth filters. Ideally, wire cloth filters provide high strength as well as abrasion and corrosion resistance. Perhaps the best thing about wire cloth filters is that they can be made with varied apertures. During the filtration process, there are also instances where plastic material has been used to serve the same purpose of filtration using plastic mesh belts as they provide an equal strength and resistance. The use of metal mesh filters allows the solid particles to be separated in terms of their sizes. In addition, it aids gas and liquid filtration during the finer filtration process.
What Happens in the Coarser?
It is in the coarser where micro filtration takes place. There are a number of materials that are used during the coarser filtration process. This process largely depends on the shape and the size of te openings in the sheet or mesh. During the coarser filtration process, there are three main media used which are; woven wire mesh, sheets perforated with a variety of holes and elements made from rods and bars.
What Is Woven Wire and Screens
Woven wire can simply be described as metal screens that are designed in such a manner that they form a round plain-weave wire. This creates one notch of durable high weave that is woven wire screen. The woven wire screen also has unchangeable mesh size with perforations of different shapes. The unchangeable mesh size is meant to create lateral and longitudinal tension. In most cases, manganese steel us used to make the woven wire and screens as it is considered to be highly durable and abrasion resistant. The mesh can range from 1, 0 mm while the wire Ø 6, 3 mm. The weaving of the wire used a traditional technique where the weft wires cross over the warp wires that are set along a loom. After this form of weaving, what comes out of it is a woven mesh that can be processed further to improve the filtration process. In layman’s terms, the woven meshes can best be described in the context of filtration as wire cloth filters.