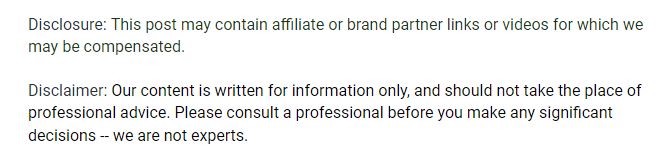

The invention of computed tomography scanning equipment (sometimes referred to as “CT scanning equipment”) occurred in 1972. Its inventors, Godfrey Hounsfield and Allen Cormack, used a compilation of hundreds or thousands of 2D x-rays to put together 3D imaging of the inside of a person’s body. This breakthrough in technology allowed doctors to run a number of tests and come to an accurate diagnoses for a patient, without having to cut them open in the process. Their computed tomography scanning technique was quickly adopted by hospitals all over the world, and Hounsfield and Cormack were both awarded Nobel Peace Prizes for their contributions to both science and medicine.
While computed tomography scanning technology has saved an unquantifiable numbers of lives in the medical industry, it is just breaking ground in the industrial industry. Having the capacity to see the inside and outside of a part, down to the number and thickness of the fibers that make it, within a very short matter of time, and without inflicting any damage to the part itself, opens an enormous opportunity for testing and quality control. A few applications of computed tomography scanning in the industrial sector include:
- Porosity Measurement
After computed tomography scans are taking of the part, the internal and external measurements are calculated, which determines the volume of each pore of the part. The range of porosity within the part is color-coded in the scans, so the pores with higher volume contrast against those with lower volume. This is instrumental in identifying weaknesses in the part at a pore level. This level of detail has never been available prior to the use of computed tomography scan in the industrial world. - Part to CAD Comparisons
With a part to cad comparison, detailed scans are taken of a part, and then compared to the computer auto drafted (CAD) plans for it. Any distinctions between the CAD plan and the actual part are identified. Any deviations that are identified can be corrected if they could lead to the part malfunctioning. - Part to Part Comparisons
Like part to cad comparisons, with part to part comparison, computed tomography scans are taken of two parts and any deviations between the parts are identified, so that the manufacturer can ensure its quality. - Failure Analysis
Using computed tomography equipment, scans can be taken every angle of a part and a cross-sectional visualization of the part and its entirety can be given to the manufacturer. This helps its creator determine any issues that could lead to failure. - Reverse Engineering
Sometimes parts are needed that are no longer being manufactured, and there are no plans available for how to build it. Using computed tomography, scans assess the internal and external measurements of the part, so the manufacturer can recreate with the exact specifics of the original. - Composite Measurements
The level of detail that can be achieved with a computed tomography scan can be drilled down to the very makeup of its fibers. Using composite analysis, the density of the material that makes the part is determined, and the difference in density between pores helps the computer distinguish its fibers. Once this is done, evaluations can be taken on the length, diameter, and direction of every single fiber in the part. - First Article Inspections
Like so many of the other valuable uses for computed tomography scanning, the in-depth level of detail that can be pulled from the scans helps ensure the quality of the first article off the assembly line. A first article inspection is conducted by running a part-to-cad comparison to identify differences between the computer plans for the part and the part itself. Other specific points that are predetermined by the owner of the part may be evaluated as well. This test is often conducted by the part’s purchaser, to ensure the quality of the product from the manufacturer before massive amounts of them are made.
Do you have any questions about the applications of computed tomography scanning in the industrial sector? Have you experienced this relatively new method of part inspections? We’d like to hear about your experience with it, and answer any questions you might have. Please continue this discussion in the comment section below.