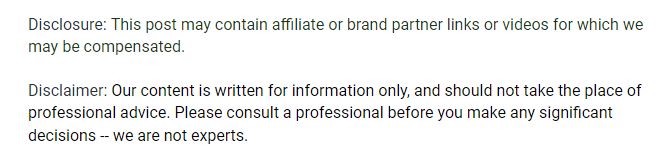

For the record, this article is NOT about polychlorinated biphenyl (the banned synthetic chemical); this is a story about the often-forgotten other PCB.
What in the world is this PCB and how can it be THAT important to me, you ask? Here’s how:
Printed Circuit Boards (PCB) are an essential component in all multi-layered technology, the little circuit board that runs your remote control, phone, tablet and other electronic devices. Seems a little more important now, doesn’t it? PCBs are one of the most efficient options for technological production–while they require a certain amount of individual design, the majority of the circuit board can be manufactured through automated systems after the design in put in place. This is similar to each company’s manufacturing process; every PCB is created and designed according to specifications as instructed by the client or company ordering them, as well as the purpose of the circuit board in the first place.
Originating as far back as the turn of the 20th Century, PCBs were primarily used by the U.S. Government during World War II. PCBs did not begin to really take use until the 50s, when the U.S. released it for public usage. Since then, there has been an explosion in utility as changes in technology have expanded the abilities and uses of PCBs. One huge breakthrough has been rigid flex circuit boards, which is made to allow flexibility during use and conformity to shape specifications.
The main ingredient used to created the base of these boards is fiberglass, which gives the boards a thick and rigid core (some companies also use a high-temperature plastic for increased flexibility.) On average, the common thickness found is about 1.6mm, while other boards can have as little as 0.8mm thickness. To put that in perspective, the average width of a human thumb nail is roughly 1.5cm, and the average thickness of the base of rigid flex circuit boards is about one tenth of that size! While most production of these boards are done through automated machines, many highly-skilled technicians are able to work these by hand, working with 0.01-to-0.02-inch pieces using a microscope, tweezers and fine-tip soldering iron.
After creating the base, copper layers are added through lamination to one or both sides of the rigid flex circuit boards (typically both but sometimes only one side in lower-cost gadgets). This usually amounts to an ounce of copper per square foot; however, some heavy-duty PCBs meant to handle high power can have as much as 2 or 3 ounces of copper per square inch. One ounce per square inch of copper translates to about fourteen ten-thousandths of an inch of additional thickness per ounce per square inch (0.0014 inch). To compare this with the earlier example, the width of the human thumb nail is 5/8 inches, or 0.625 inches.
Needless to say, manufacturing rigid flex circuit boards and other PCBs is a very complex task. Obviously, this leaves plenty of room for error, most of which is detrimental to the entire circuit board. For example, not insulating two 0.01-inch metal traces as needed can lead to an arc with chars and destroys the entire board. In general, PCB failure can be caused by two issues: environmental stresses and design failures which can both lead to serious performance problems.
However, design issues are far and few in-between, as most of the world’s technology (and the people who use it) rely on consistency and expert design in order to function and interact with each other. So far this hasn’t been too much of a problem either–revenue collected in 2014 by circuit board manufacturers, including semi flex PCB suppliers, reached a whopping $44 billion, and with the exponential rate at which technology is shaping and affecting our world, that number is sure to increase just as fast.
Leave your thoughts and questions in the comments section below!