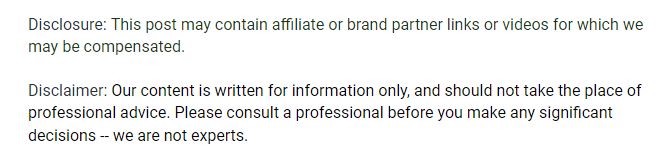

Most people have visited a hotel before. You also have probably noticed the housekeeping staff as they move from room to room, cleaning each room for the next night?s guests. They transport all of their housekeeping supplies, such as the towels, sheets and cleaners with a rolling laundry cart. Without this cart, they wouldn?t be able to hold all the items they need. You probably didn?t give much thought to the housekeeping staff, and probably even less thought to the laundry cart they were rolling down the hallway. That rolling laundry cart is a necessity for the staff and has provided many benefits to the cleaning staff and the hotel management. A lot went into the planning and the development of that commercial laundry cart on wheels.
Rotational Molding is an extremely specialized and unique process. Heat is used to melt and fuse plastic resin in a closed mold. Unlike most other plastic molding processes, no pressure is involved. The four-stage process includes loading the resin in the mold, heating and fusing the resin, cooling and finally unloading the part from the mold. All of these steps must be taken when producing the rolling laundry carts. The same process is also used for other common, necessary products.
Recycling carts, similar to the rolling laundry cart must also be designed and produced in a similar way. Time is also needed in the production of these beneficial products. While the actual duration depends on the complexity of the design, and the approval process, the typical development timeline is: 6-12 weeks for tool build, 1-3 weeks for inspected samples, 1-3 weeks for finished part evaluation (total 8-18 weeks). Most people probably would never realize that those industrial laundry carts took so long to build!
This is the same process that would be used to create other types of products. Molding is done to shape the plastic or the metal into the shape of the product needed. Inventors and designers will work with the molding team to reach a satisfactory product. This process could take even longer, when an item is not already planned out. Fortunately, the molding process is good for all sizes and weights of products. Rotational molded products can be as small as a ping pong ball and as large as a 20,000 gallon tanks. Some services are capable of manufacturing products from 0 to 1,000 pounds in weight and up to 17 feet long.
A lot goes into the design and the production of many common products. A simple rolling laundry cart that is used daily by hundreds of thousands of housekeeping staff has to go through a design and then a production process. Recycling carts much also go through a similar process. Molding is the process of melting down and then shaping metals or plastics into the shape of a needed product. Molding is able to accommodate all sizes and shapes of products. It can hold weights up to 20,000 gallons and as small as 0 pounds. The world of molding and creating products is very complex and distinctive.